Microscopic Particles Cause Catastrophic Failure
It is a common scenario for machinery using hydraulic systems for transmitting power: a microscopic solid particle causes catastrophic failure of a component. According to industry experts, contamination causes 65-90% of all hydraulic system failures. The malfunction may be intermittent, requiring extensive troubleshooting to identify the faulty component.
Once identified, the component must be removed for repair or replacement- another time-consuming and often messy task. During all this time, the machinery is out of service, resulting in lost productivity and corresponding profits. In order to prevent a recurrence, the source of the contamination is investigated, and often the cylinder is a prime suspect.
Due to relatively large internal volumes and manufacturing processes, new or repaired cylinders have developed a reputation for harboring destructive hydraulic fluid contamination. Consequently, when a sensitive valve or pump fails, the finger is often pointed at the cylinder manufacturer.
Preventing Hydraulic Cylinder Contamination
Cylinder manufacturers must create and follow strict processes to prevent a hydraulic cylinder from contributing to the failure of other system components such as valves and pumps.
Step 1: Identify Contamination Types Specific to Cylinder Manufacturing
The first step is to identify the common types of hydraulic system contamination specific to the manufacturing process.
- Category 1 – Hard Particles: Hard particles include various types of metal, such as steel, iron, bronze, or aluminum, which may be generated during cutting, machining, grinding, or welding. It also includes dust and dirt. Airborne dust can settle on the surfaces of the internal cylinder components before assembly. Granular absorbents are especially troublesome because they swell and clump when oil is absorbed. Larger hard particles can cause sudden and severe damage, such as cutting seals and scoring metal surfaces. Smaller hard particles, also called “silt,” can be equally destructive but gradually cause wear and damage over a longer time period.
- Category 2 – Soft Particles: Sources of soft particles during cylinder manufacturing include rubber or urethane seals, composite bearings, and cloth fibers. These soft particles typically cause failure by clogging orifices or small passageways.
- Category 3 – Water: Water can be introduced from a humid environment or component parts that are not fully dried after cleaning, and it can cause corrosion and microbial growth.
Step 2: Stop Hydraulic System Contamination at the Source
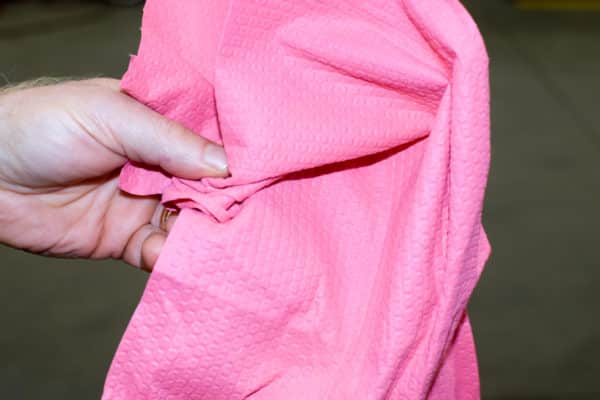
After identifying the potential sources, the cylinder manufacturer can take steps to prevent building contamination into the cylinder during the assembly process. Although cutting and machining processes are necessary, the parts can be cleaned thoroughly. Work surfaces, storage locations, and material handling devices can be kept free of dust, dirt, and metal particles. Parts that have been cleaned can be kept in sealed plastic bags or covered with plastic to prevent re-contamination.
Climate control and air filtration systems can limit airborne dust and humidity in areas where cylinders are manufactured. Implementing procedures to completely dry parts after cleaning can ensure the moisture does not become a contaminant. Because common shop rags and disposable towels are notorious for shedding lint and fibers, selecting lint-free shop rags, disposable wipers, and absorbent mats can limit the introduction of soft fiber contamination. Granular absorbents should never be used in a hydraulic component manufacturing facility.
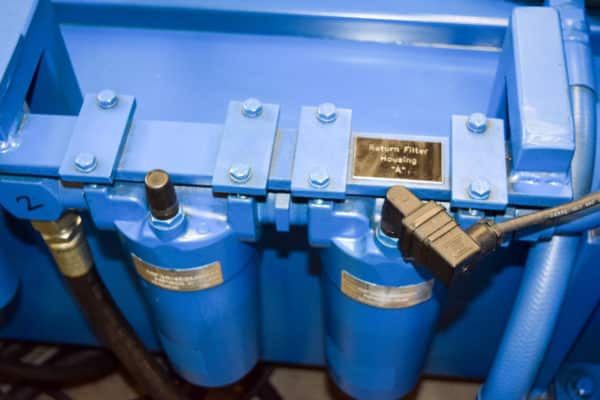
Step 3: Remove Contaminants That Eluded Preventative Measures
The last line of defense is to remove any hydraulic cylinder contamination that eluded the preventive measures before providing the complete cylinder to the customer. Functional testing is standard to check for internal or external leaks and ensure the cylinder provides the correct stroke. As the cylinder is cycled during the test procedure, hydraulic fluid flushes out contamination built into the cylinder.
While it is beneficial to remove particles from the cylinder, the result is a spike in the contamination level of the test stand hydraulic fluid. To prevent contamination of future cylinders, the test stand system can be equipped with hydraulic filters to remove the particles from the fluid.
Hydraulic filter manufacturers have developed high-performance filter elements that effectively remove microscopic particles, even down to 1 micron. The best strategy is multiple filters at different locations in the system.
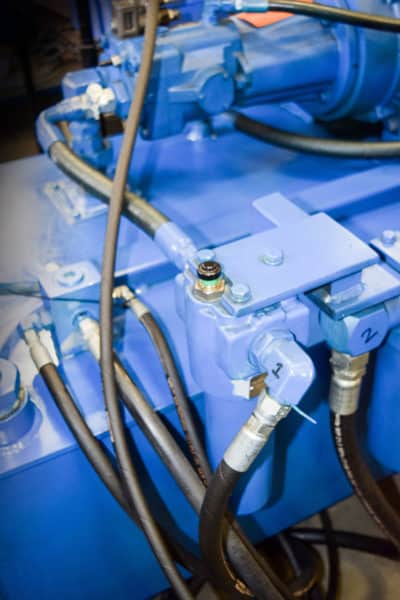
Return Line Filter
The highest priority filter location is in the return line, so hydraulic cylinder contamination that is flushed out of the cylinder can be immediately captured, keeping the fluid in the reservoir clean. Whenever a return filter is specified, the size should always be designed for the maximum possible return flow, considering the pump flow is multiplied by the ratio of the blind area to the annulus area. A hydraulic cylinder test stand will be expected to test various cylinders with ratios ranging from 1.1:1 to 10:1. The return filter should be sized based on return flow from the highest ratio cylinder being tested.
Pressure Line Filter
The next location is in the pressure line, generally after the pump and before the directional control valve, to ensure the fluid going into the cylinder being tested is as clean as possible.
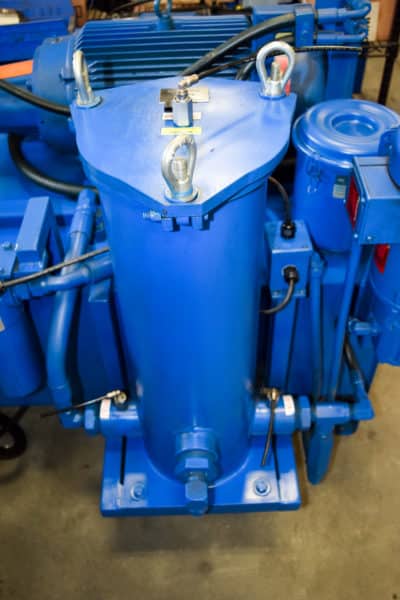
Kidney Loop
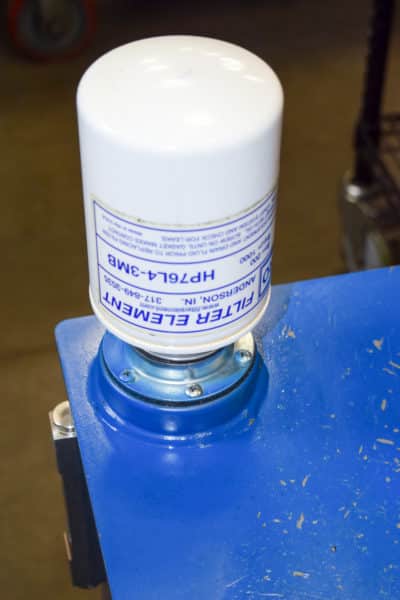
Ideally, the system will also include a low-pressure offline circuit that operates at a consistent flow rate, independent of the main test stand hydraulic system. These subsystems are designed for the sole purpose of conditioning the fluid. If the fluid becomes contaminated, the kidney loop can filter the fluid to prevent damage to the high-pressure components in the test stand hydraulic system.
Reservoir Breather
This critical piece of the filtration puzzle is often overlooked. Each time a test cylinder is extended, air from the surrounding atmosphere is drawn into the reservoir. Inexpensive, coarse cellulose or foam media will allow a high percentage of particles less than 10 microns to pass, increasing the contamination of the fluid. Select breathers that closely match the fluid filter’s micron rating and replace them regularly to meet your targeted cleanliness levels.
Significance of Cleanliness Standards
Regularly measure and monitor the cleanliness level of test stand fluid to confirm the filtration system is functioning properly and remove the hydraulic system contamination that is introduced with each cylinder test. The most widely accepted standard is ISO 4406, which provides a three-digit format reporting the number of particles greater than 4, 6, and 14 microns in a given volume.
For example, an ISO code of 17/15/13 indicates 640 to 1,300 particles greater than 4 microns per milliliter, 160 to 320 particles greater than 6 microns per milliliter, and 40 to 80 particles greater than 14 microns per milliliter. This format can be used to define the cleanliness level of a given fluid or specify the desired level. It is also common for hydraulic component manufacturers to publish a maximum allowable contamination level for their products.
Because even particles that are too small to see can cause damage, visual examination of the fluid is not adequate. The accepted conventional methods available for analyzing fluid include gravimetric, laboratory analysis, and inline particle counters.
- Gravimetric: The gravimetric method is passing a sample of the fluid through a patch that captures the particles, then weighing and examining with a microscope. This method is relatively labor-intensive and typically has a high margin of error.
- Laboratory Analysis: Another option is to collect a bottle sample and submit it to a laboratory for analysis, which in addition to particle count, can check the viscosity, water content, composition of the contamination, and several other factors. While the results are comprehensive and accurate, there is a time delay until results are received. For example, if a sample is taken and two days later the report indicates a problem with the fluid, all cylinders tested during those two days are at risk of being contaminated.
- Inline Particle Counters: [DSC_0111-2] An inline particle counter directs a laser through a stream of fluid and sensors detect the size and number of particles, providing continuous and immediate detailed particle count reports and ISO cleanliness codes. This real-time information can drive actions, for example, waiting to test until fluid cleanliness has improved. The test of a specific cylinder can also be associated with a fluid cleanliness level, which may be useful in case of a warranty claim. The data can also provide feedback on the effectiveness of continuous improvement initiatives to improve cleanliness.
Reduce Your Risk of Hydraulic Cylinder Contamination
Machine OEMs and End Users should take measures to prevent costly and time-consuming hydraulic failures. In addition to installing and maintaining hydraulic filters, preventing ingression of particles into the system, and excluding moisture, it is also beneficial to consider contamination when selecting a hydraulic cylinder supplier.
Specifically, choose a manufacturer who understands the risk of hydraulic cylinder contamination and has implemented appropriate standards and procedures. These preventive measures should start when the first piece of material is cut by a saw, continue through machining and welding, and carry through all the way through the completion of functional testing. These precautions require investment and commitment by the cylinder manufacturer; likewise, the customer should look beyond the purchase price of the cylinder and consider the much larger value of reducing the risk of contamination related failures.
Are destructive contaminants hiding in your new hydraulic cylinder?
It has been said that cylinders are the top contributor to hydraulic system contamination. You can help prevent hydraulic system contamination and costly repairs by using Purpose-Built™ hydraulic cylinders manufactured with quality and cleanliness.
Aggressive Hydraulics’ Culture of Cleanliness means we take extra steps to avoid hydraulic fluid contamination during manufacturing. We hold each product we manufacture to high standards and have implemented a Fluid Cleanliness Program that exceeds top OEM requirements. Our investment in the Fluid Cleanliness Program is an investment in your business.
Call or send us a message to learn more about our custom cylinders and how they help reduce the risk of hydraulic system contamination stemming from the cylinder.